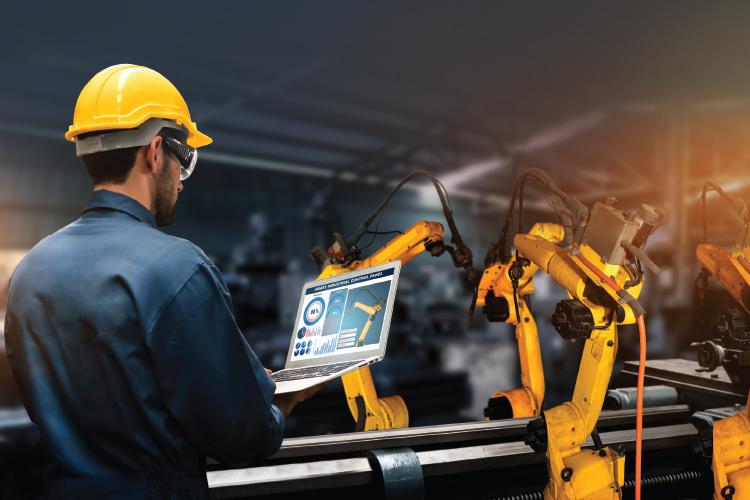
It was in 2011 that the term, Industry 4.0, was first used in Germany. A year after, Germany—a global leader in manufacturing—created a working group, which presented a set of recommendations to the federal government on Industry 4.0.
However, the idea became popular worldwide, when, in 2016, the World Economic Forum (WEF), chose Mastering the Fourth Industrial Revolution the theme for its annual meeting. It was not just another annual theme for the organization. WEF Chairman and Founder, Klaus Schwab, actively evangelized the idea and has since written a book on it, explaining its concept and impact.
In essence, Industry 4.0, as a concept aims for seamless fusion of the digital and physical—and is very often explicitly identified with the use of sensory technologies like IoT in industrial operations.
Many describe it as the digital transformation of the industrial sector—which includes manufacturing, mining, oil & gas, heavy construction among others—which not long back lagged the services industry in terms of digitization. Though point automations existed, use of IoT and the (desired) coming together of Information Technology (IT) and Operational Technology (OT) promised a whole new paradigm—of smart, self-maintaining manufacturing operations.
The beginning
After the WEF evangelized it, Industry 4.0 became a buzzword for manufacturing CEOs globally. The interest led to small experimentations. But the ground conditions were not yet conducive. As always with such cases, the term was abused, with any automation exercise being labeled Industry 4.0 initiatives.
It was still a promised land.
Yet, all that hype had its positive effects.
One, a few companies took it seriously and started experimenting. Some of those worked and some did not. The few that worked created more hype.
Two, many manufacturing, oil & gas, construction companies started deploying IoT sensors, if not for anything else, just to show the top bosses that something was happening (well, that is a bit harsh view, but not entirely untrue). But even those limited deployment showed tremendous impact in some cases, creating a positive halo around the concept in an otherwise skeptical and conservative sector.
The biggest thing it did was that it converted the CEOs from digital-open to digital-converts. It was no more the CIOs who were talking of digitization—and were being rebuffed by the manufacturing operations people. It was the CEO who dreamt digital.
That was quite a change. It was the same change cloud brought in enterprise IT—CFOs (and in a few cases CEOs) were asking for it.
Technology companies, with their allies, the CIOs, grabbed the opportunity to turn the conversation into a use-case conversation. Once it became use-case conversation, talking to the business users—read manufacturing operations managers—became much easier. While the conversation with the CEO was still the topline, bottom line and digital transformation, the discussion with the plant managers was around their challenges and how Industry 4.0 would solve those problems comprehensively.
Be in no doubt. We are talking about the conversation. The real implementation was still some time away, thanks to the proprietary OEM equipment being used in manufacturing. These OEMs were slow to change. And suddenly, security—as manifested by the now famous IT-OT integration issue—became the central talking point.
But at least, the conversation had moved from concept to implementation stage—no matter how challenging the situation was.
Pandemic as the game changer
Last one and half years changed everything. The pandemic struck at a scale never seen before. And as widely acknowledged now, it has had a positive impact on digitization all across – in our personal lives, governance, public services and businesses.
Manufacturing industry was no exception. Unlike services industries, it was not possible to shift lock, stock, barrel to remote working. So, some quick, tactical digitization happened. Supply chain in general and approvals in particular saw quick digitization in many organizations.
But the more important—though subtle—impact was somewhere else. The pandemic forced the senior executives in manufacturing businesses, some of whom depended on their secretaries to check their e-mails, to use collaborative tools, if nothing else, to keep the business running. And soon they discovered, digital was not such a tough thing, after all.
While the now common joke—neither CIO nor CEO but COVID was the biggest driver of digital transformation—has a real basis, some CXOs became ‘digital savvy’ (a senior CFO’s own word) overnight.
In India, many top executives in the manufacturing industry looked at China with awe when many plants started operating in an almost unmanned fashion, thanks to years of automation. These workerless factories forced many CXOs in manufacturing companies to realize—and guess what admit—that there is no alternative to Industry 4.0.
Another interesting parallel development happened. Industrial equipment suppliers—Original Equipment Manufacturers or OEMs, as they are commonly called—too realized that they can no longer lag behind. Some of them launched new initiatives and even acquired companies to provide digital solutions for their clients, the industrial sector.
The technology conundrum
Before we get into what is happening—and why and how it is happening—we have to have a little flashback.
The effort to make IT and OT talk to each other is not new. Businesses, in order to collect data from manufacturing systems for analysis for long-term business decisions, have been trying to make the data flow smoother. But despite all efforts, the effort did not make much headway and the issue is still, to a great extent, unresolved. Ask any manufacturing CIO anything about digital transformation and the discussion will invariably get into IT-OT integration. Security professionals are even more vocal about it, citing the vulnerabilities that these proprietary OEM equipment have.
Interestingly, the concern about security is also echoed by the manufacturing professionals. As Santayana famously said, when men and women agree, it is only in the conclusions. Their reasons are always different.
While the issue before the IT and information security professionals are vulnerabilities in the older OEM equipment—some of them still running on Windows XP—the concerns of manufacturing professionals has been around their protected, ‘safe’ closed manufacturing systems being exposed to external threat that is so common in the IT world, or as security experts would put it, widening the attack surface. Many industries that are marked as critical infrastructure by the government are even more cautious.
Ironically, both the camps are right. But the time is more on IT’s side, as a decision not to make IT-OT talk, means no change to status quo. That is not the preferred path in a competitive business environment.
But all through, these arguments to change were always put forward from the business side, with the CIO being seen as the champion. There was very little for the manufacturing professionals, those managing OT. All they were hearing is to go after their OEMs pushing the latter to change and adapt faster.
To some extent, the pandemic had some impact on that, as the vendors accelerated their digital strategies.
Also, the low hanging fruits – digitization of warehouse/inventory, logistics, security – which were taken up convinced them (the OT owners) the definite advantages.
The IT suppliers too figured out that they have to address the needs and concerns of the manufacturing systems owners and show them the benefits of digitization—in a manner that would appeal to them.
Enter the edge
It is then that the IT industry turned to the new mantra in technology deployment—find use cases.
This search for use cases—many of which we will discuss here—threw up a technology that was there, but not yet ‘there’— meaning it is nothing new as a concept but quite overshadowed by the dominant cloud model which has been ruling the enterprise tech zeitgeist.
That technology is edge computing—a term used for use of computing and storage in close geographic proximity to the place where data is generated, so as to enable the processing faster, especially if the processed data has to be used in that location itself for taking an operational decision. It can enable fast data processing and reduces the need to transfer large amounts of data across the network.
It is called edge, because in terms of traditional network where centralization of data storage and processing is the norm, this computing resource is located at the periphery or edge of the network. While telecom operators, data center service providers, cloud providers and enterprises all have their definition of the edge, from their operation’s perspectives, in this article, we will refer to ‘edge’ as the enterprise edge—that is wherever the computing resources are located close to where data is generated within the enterprise. Wherever there would be any reference to service providers’ edge, we will explicitly mention that.
In manufacturing industries, which is the focus of the current discussion, the data capture devices such as IoT sensors are also often called edge devices. But by saying only ‘edge’, we will refer to edge computing - that is distributed computing and storage resources in the premises of the enterprise (in this case mostly, manufacturing) campuses.
According to Gartner, by 2025, 75% of all enterprise-generated data will be created and processed outside a traditional centralized data center or cloud—up from just 10% in 2018. Gartner defines edge computing as solutions that facilitate data processing at or near the source of data generation. In the manufacturing with IoT sensors, the sources of data generation are usually things with sensors or embedded devices. It further says by 2023, 50% of large enterprises will have a documented edge computing strategy, compared to less than 5% in 2020.
Why edge matters in manufacturing
Edge computing is not a new concept. It is geographically distributed computing by another name. The renewed interest in edge computing in the last few years is because of the new automated model that is the foundation of Industry 4.0, though its application in other areas—especially in public services as in smart cities—too is significant.
This new automation model consists of data collection by sensors often with an aim to use (of course, after processing and analyzing) that data in near real-time.
This necessitates the need for analyzing the data geographically close to the place where it is generated. This is fundamentally because of two reasons – large volume of that data (much higher than any human generated data) and the need to quickly analyze that data. Both these compel technology managers look for a model that minimizes bringing data back and forth.
That model is edge computing.
Why edge computing has become such an important technology for transformation to Industry 4.0 becomes clearer when one looks at the fundamental components of Industry 4.0.
There are five broad areas of Industry 4.0 application:
- Sensor technologies for data collection
- Higher levels of automation such as deployment of robots
- Analytics, AI/ML for operational decision making
- New ways of human-machine interaction such as augmented reality and virtual reality
- Advanced engineering such as 3D printing, better material testing, quality improvement, energy efficiency and optimization of engineering design such as cost analysis and planning
Edge computing facilitates all these. It makes it possible to do near real-time analysis effectively by minimizing on the time and volume of data transmitted in long distances and doing most, if not all analysis, at the plant site.
In more specific terms, the drivers of edge computing in manufacturing include:
- Need for real-time analysis. Very often operational decisions such as those on production and maintenance have to be taken for efficiency, productivity, better production quality and even plant safety. Time is of essence and transferring large amount of data to distant centralized data centers or the cloud may not be the best way to do it.
- Need for low latency applications. While most operational decisions do have some time sensitivity, some of them are really critical. A little delay may result in huge downside. Such applications like, say visual analytics for safety and security, may not even be feasible by relying on a distant computing and storage infrastructure, considering the physical limitations of the currently available transmission speed.
- Better security. Sending data over long distance potentially exposes it to security threats. But more than that, what manufacturing system owners are worried about is direct connectivity of manufacturing systems to the outside world. It is especially true in sectors having critical infrastructure, such as oil & gas, ports, and power. More connectivity with the outside world—especially for core manufacturing systems—increases the threat surface significantly.
- Lack of connectivity. A peculiar problem for manufacturing, especially in India, is the location of manufacturing plants in remote areas – places close to availability of raw materials, coal and cheaper labor. Many of these places lack basic connectivity. So, sending data in near real-time may not even be possible, let alone other issues like time sensitivity and security.
- Reduction in volume of data transmission. Even if some places have basic data connectivity available, the large volume of data that need to be generated to be able to analyze that in near real-time may not be feasible considering the quality and cost of connectivity.
It is no surprise that experts see manufacturing sector being a nig user of edge (in conjunction with 5G, more about that later) technology. According to KPMG, by 2023, five industries will spend more than USD 500 billion on what it calls 5G+Edge ecosystem. Out of that, USD 206.4 billion or some 40% will be spent by industrial manufacturing sector.
Why now? What changed?
We have discussed what prevented the manufacturing companies from going all out for digitization. The crux of the problem—if it can be said so—was the force of digitization, despite the CEOs’ digital conversion was not strong enough to defy the force of gravity. It was not enough to address the challenges perceived by the people who own manufacturing system and thus in charge of operational technology.
So, what changed in the last couple of years that now makes it seem the Industry 4.0 dream is for real?
AI as the driver
Well, the German computer scientist, Wolfgang Wahlster, who is credited with coining the term Industry 4.0, is actually an AI expert. But AI itself was never mature enough to be put into application in areas that require analysis of a lot of critical, real-time dynamic data, in various areas like visual analytics. That has changed.
And the technology industry did good enough to create compelling use cases to show the manufacturing system owners what is possible. Look at the use cases listed in the box. Most of them would not be possible without advanced analytics and AI.
While the promise of better security may have lured manufacturing professionals to edge computing, what has made it possible is the promise—and demonstration—of what is possible using AI.
5G as the enabler
5G is not here yet. And manufacturing organizations have started testing newer Industry 4.0 application using edge computing and storage. But most of these have been point applications are often glorified pilots.
But any large manufacturing company—typically conglomerates in India—that is seriously formulating an edge computing strategy has 5G built into that.
A word of caution, though. Though ultimately, they will figure out what works best for them and what works, today, there is a confusion regarding what edge is among many technology managers in manufacturing company. The enterprise definition of edge, the telco’s definition of edge and the data center/cloud service providers’ promise of edge are all different ideas.
As clarified above, throughout the story, we have taken edge as enterprise edge – where the computing and storage is located close to, typically inside the manufacturing campuses. Telcos and technology vendors play a significant role in it. And one will not be surprised if smart data center service providers get into that game too. But the ‘edge’ should always be relative to the enterprise’s core – or central IT infrastructure, be it on-premises/collocated data centers or public cloud.
How does 5G help? Simply speaking, being an end-to-end IP network with high-speed radio at the core, it helps a manufacturing enterprise connect its plant machinery, especially the moving assets, to the computing and storage resources in the campus. This 5G network could be owned and operated by large manufacturing companies themselves or by external operators in a virtual captive mode or using public telco’s 5G. 5G will also make it possible to take high speed long haul to manufacturing sites, where taking fiber was not feasible, both in terms of cost of laying and maintenance.
Being a wireless technology, some of the assets which are movable and which are forced to be static but can provide more flexibility as movable assets could be connected using it.
We may see a huge uptake in edge computing once 5G becomes available. The telcos will surely play a major role.
Pandemic as the accelerator
As discussed in the beginning, the pandemic demonstrated the value of digital to all in the organizations, across sectors. So, some inhibitions are diluted. But the most visible change is that if forced the manufacturing OEMs to change finally. Many large OEMs have already undertaken branded programs to accelerate digitization and modernization of their equipment. This change in mindset, accompanied by some efforts towards standardization and interoperability, will accelerate the move.
Technology companies as the facilitator
Technology companies have to play—and they have done that to some extent—two roles.
First, they have to help the CIO in convincing the OT owner, which they have been doing using use cases and creating solutions for specific applications. HPE’s focus on Aruba line of products, is a case in point. Aruba products are things that operational people can relate to far better than the traditional IT stuff like storage, computing and networking, which CIOs are comfortable.
Second, many technology equipment companies, including the likes of HPE, Dell, and IBM, now realize that this is their best opportunity to get back to the market, which they were losing to cloud providers. For that, they also have to convince the CIOs, who are getting too cozy with public cloud, because it gives them easier manageability, variable cost, seamless technology upgradation. Top vendors now promise the same with their equipment, which they are more than eager to lease, manage and of course, upgrade as in cloud—while appealing to the operational technology owners through their ‘better security’ pitch. This model, now branded by many vendors, is a serious and aggressive offering.
The cloud service providers and the data center service providers have not given up yet. While the hyperscalers are trying to partner telcos—as we have seen in case of AWS and Verizon—the local service providers see this as an opportunity to get back to the game. Many are promising edge data centers as their differentiators, which hyperscalers would find difficult to provide. In India, the Central Government’s Data Center Policy too encourages this model of edge data centers at various locations.
Edge computing, combined with 5G, may finally make the Industry 4.0 dream getting realized. Globally, manufacturing companies are definitively tilting towards edge computing. It seems India is now ready for the game.
Add new comment