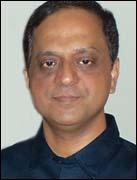
Started in 1977 in South India as a small manufacturing unit for voltage stabilizers, V-Guard Industries is today a leading maker of stabilizers, pumps and motors, electric water heaters, solar water heaters, cables, UPSes, and ceiling fans. With a network of nearly 200 distributors and service centres and above 9500 retailers, it serves the needs of over 50 million customers.
Business and technology challenges
With an annual growth rate of 35 to 40 percent, V-Guard was facing multiple challenges. The IT systems were in-house developed and could not cope with the changing needs. IT penetration was not uniform and inventory and financial accounting used to happen via IT application, whereas production activities were monitored in some stand-alone systems and costing was entirely an Excel-based system, says Robin Joy, CIO and General Manager, V-Guard Industries Ltd.
Maintaining skills for development and support of legacy application was also a big challenge, he says. Profitability analysis, a key parameter for V-Guard Industries as far as pricing of products is concerned was not happening in a proper manner.
The Solution
To tackle these challenges, V-Guard decided to deploy SAP software with the help of implementation partner IBM.
We had evaluated a few tier-1 and tier-2 companies as SAP partners. As an SAP implementer, IBMs credentials are well known and established by the countless number of SAP implementations they have done. We had also put up a stiff challenge of completing track-1 of SAP implementation in less than 6 months time. IBM took the challenge well and prepared a plan for fast-track implementation, says Joy on choosing IBM.
The companys expertise on similar industry segments and successful implementations in South India also scored in its favour. Finally the IBM pre-sales team did a wonderful job in preparing a business case (though very brief) which helped us to appreciate the benefits and guided us to understand how our expectations would be answered in the process, says Joy.
V-Guard chose IBMs Ascendant Methodology for SAP implementation. The scope of the project covered all the logistics modules, SAP HCM and Business Intelligence and Business Optimization.
The Benefits and RoI
The biggest success was the seamless integration V-Guard achieved through this implementation. We have real-time view of our entire manufacturing locations and depots with financial and operations. It provides better visibility into costs through product costing, thereby providing levers to manage costs and also provides with seamless integration of manufacturing, logistics and accounting, says Joy. According to him, the benefits include:
- Fully integrated business processes SIPOC (Supplier, Input, Process, Output, Customer - covering all major business processes for procurement, inventory management, requirement planning, sales and distribution, finance and controlling)
- Visibility and analysis of actual costs
- Profit-centre and segmental reporting for more accurate internal and statutory reporting
- Segmental and product-wise profitability analysis to effectively monitor Key Performance Attributes
- Integrated and real-time tracking of Quality Management, Plant Maintenance & Customer Service activities
- Human Resources and Payroll processes integrated with key business processes such as Finance and Costing
- Harmonization of system landscape involving Oracle, IFMAS and other in-house applications, on to a single and centralized SAP ERP system
- Business Intelligence/Business Optimization Reports for Management (covering all Important KPI reports for performance analysis and performance management)
Doing things differently
To meet the challenge of tight project timelines and schedule, and to reduce the overall risk exposure during V-Guards sales season, the company split the implementation project into two tracks, says Joy.
Track-1 consisted of SAP Sales and Distribution, Materials Management and Finance modules and Track-2 consisted of Controlling, Production Planning, Quality Management, Plant Maintenance, Customer Service, Human Capital Management, Business Intelligence and Business Objects.
The first track was scheduled to go live on 1st February 2012 and Track-2 was scheduled to go live on 1st April 2012, resulting in a gap of two months between the two tracks. V-Guard business was expected to operate on SAP and legacy ERP application during the interim period, says Joy.
Recounting the challenges faced, Joy says: During the Business Blueprint stage, we realized that there would be an enormous increase in workload by way of the reconciliation process for Financial & Inventory transactions during the interim periodthe period between Track-1 and Track-2 project go-liveresulting in a complicated year-end closing activity. We decided to advance the go-live of critical modules like Production Planning, Controlling and Quality Management from Track-2 to Track-1 based on extensive analysis carried out by IBM and V-Guard Project Management team, which resulted in reducing the overall workload and complexity of dual data entry on two ERP applications.
This change in implementation plan really helped V-Guard in a smooth transition from legacy ERP application to SAP.
Harnessing the new platform
V-Guard is planning to optimize the new platform as a key business enabler. The company has clear data on SAP usage in each location, including the number of hours of SAP operation at each end. This indirectly gives us an idea of the work to be done on the SAP system at a transactional level. To scale up the volumes, it is possible now to estimate the number of man hours required to do most tasks in SAP and, consequently, what job can be done in an 8-hour shift. This should help on new work definition and better utilization, says Joy.
On the sales front, SAP provides an availability check, which considers the stock-in-transit and stock-in-purchasing along with the stock-on-hand in predicting availability. This feature indirectly helps us to identify our constraints in supply chain and efficiencies. By proper monitoring it should be possible to improve our inventory cycle time and enable better servicing of orders, notes Joy.
Overall, things have been better at V-Guard. After the implementation of SAP, everything has become smooth. Previously, the sales module seemed to be a difficult thing to achieve but now it is a reality. Apart from that, a lot of other things like purchase control, tax documentation, statutory duties records, credit control, etc. have become easy and strong, says Joy. Besides applauding his own project team, he credits IBM a lot for the projects success, saying that the company gave it due importance and was fully involved in implementation.
Going forward, V-Guard is expecting to see a lot of other positive changes happening in the next four-five months.
Add new comment